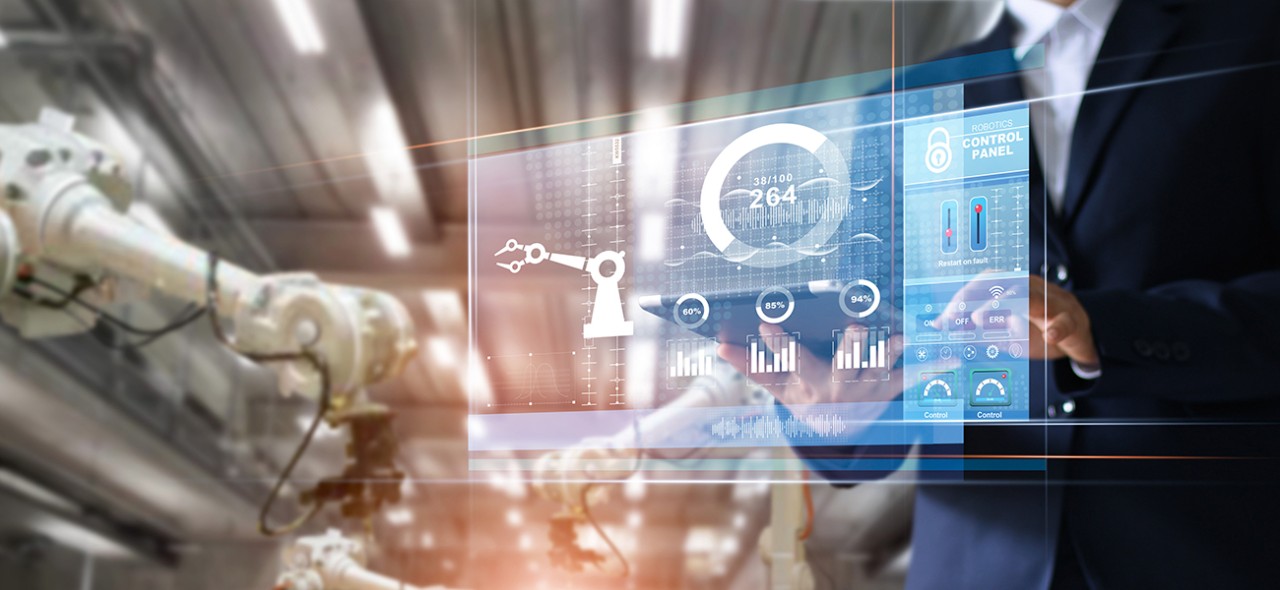
.
Understanding Manufacturing Analytics Software
Manufacturing analytics software collects, processes, and analyzes large volumes of data generated from various sources such as machinery, sensors, and production lines. By leveraging this data, manufacturers can gain insights into equipment performance, process efficiency, product quality, and supply chain management.
Factors Influencing the Cost of Developing Manufacturing Analytics Software
Scope and Complexity: The broader the scope and complexity of features, the higher the development cost for manufacturing analytics software.Basic systems focus on monitoring and reporting production data, while advanced solutions integrate predictive analytics and real-time monitoring.AI-driven decision-making is also a key feature in more advanced manufacturing analytics software solutions.
Custom features, such as integrating with legacy systems or cloud platforms, also add to the complexity and cost.
Software Features
Data Integration: Connecting the software with multiple data sources (sensors, ERP systems, and other enterprise software) can be resource-intensive.
Data Visualization: Visualization tools like dashboards and charts are essential for presenting complex data. Custom dashboards that offer real-time updates and interactive features tend to raise costs.
Machine Learning Algorithms: Incorporating machine learning and AI for predictive maintenance or process optimization requires significant expertise and increases both development time and cost.
Reporting Tools: Generating detailed, automated reports that provide insights into various production metrics is often a core feature, but enhancing these tools for customization or real-time reporting adds to expenses.
Open-source technologies lower costs but need more time, while proprietary solutions offer advanced features with licensing fees.
Specialized skills, such as machine learning expertise or deep knowledge of manufacturing processes, may come with premium rates, adding to the overall cost.
Deployment and Integration
Integration: Connecting the analytics platform to existing enterprise systems, machinery, or cloud platforms can be time-consuming and costly.
Deployment Ensuring the system is set up either on-premise or in the cloud, followed by final tests.
Cost Estimate: $15,000 – $40,000, depending on infrastructure complexity.
Post-Launch Support and Maintenance
Ongoing Support: This phase includes fixing bugs, providing updates, and ensuring smooth operation.
Cost Estimate $5,000 – $15,000 annually, depending on the level of support required.
Estimating the Total Cost
Based on the factors discussed, building a manufacturing analytics software typically costs between $100,000 and $500,000. The final figure depends heavily on the complexity, scalability, and customization required for your specific manufacturing processes.
Small-Scale Projects: For basic analytics software with limited features and data integration, costs may range from $50,000 to $100,000.
Mid-Scale Projects: For medium-sized manufacturing companies requiring real-time data, machine learning algorithms, and extensive data visualization, the cost typically falls between $150,000 and $300,000.
Large-Scale Projects: Large manufacturers that need highly customizable, AI-driven analytics systems may spend $300,000 to $500,000 or more, particularly if the system is integrated with IoT devices and uses advanced AI models.
Cost-Saving Tips
Prioritize Features: Focus on must-have features for the first version and consider adding advanced features in future iterations.
Opt for Cloud Deployment: If infrastructure costs are a concern, consider deploying the software in the cloud to save on server expenses and maintenance.
Leverage Open-Source Technologies: Using open-source frameworks and tools can reduce upfront costs while still providing flexibility.
Outsource Development: Hiring an offshore development team can significantly reduce development costs without compromising quality if you choose a reputable vendor.
Conclusion
Building manufacturing analytics software is an investment that can deliver immense value by enhancing operational efficiency, improving product quality, and reducing costs. However, the total cost can vary depending on various factors like scope, complexity, and technology stack. By carefully planning your project, focusing on critical features, and choosing cost-effective development strategies, businesses can ensure they get the most out of their investment while staying within budget.
Developing the right software can give your manufacturing operations the data-driven insights needed to thrive in an increasingly competitive market.